Micro centrale DCC modulaire - Module principal de puissance
Ce module principal de puissance, à lui seul, fonctionne comme la micro centrale DCC minimale. Associé à un ordinateur et au logiciel JMRI, il est capable de commander tous les décodeurs connectés aux rails du réseau ferroviaire (motrices, aiguillages, signalisation, animations...).
Ce module dispose de différents connecteurs latéraux lui permettant d'ajouter de nouvelles fonctionnalités par la connexion de différents montages électroniques (manette Bluetooth, suivi de la consommation de courant...). Le module de manette BLE notamment, permet de rendre ce module complètement autonome : l'ordinateur n'est plus nécessaire en exploitation.
Caractéristiques
Les nouvelles fonctionnalités apportées par cette version sont les suivantes :
- Ajout d'une détection de présence d'une locomotive sur le tronçon de programmation ;
- Ajout d'un régulateur 5V afin de ne plus être tributaire d'une alimentation par l'USB (en prévision d'un pilotage par le réseau WIFI) ;
- Ajout d'un connecteur de mesure du courant analogique ;
- Ajout d'un connecteur de mesure du courant numérique ;
- Ajout d'un connecteur de pilotage sans fils (BLE ou WIFI) ;
- Ajustement des résistances de protections des LED en fonction de la couleur afin d'harmoniser la cohérence visuelle de la centrale.
Maturité :
État d'avancement du projet
Évolutions
Schéma électronique
Le cœur de ce montage est une carte Arduino Nano v3. Son microcontrôleur est chargé du programme DCC++ adapté aux caractéristiques de ce circuit.
Les commandes sont envoyées au microcontrôleur soit par la liaison série (USB) depuis un ordinateur sur lequel tourne le logiciel gratuit JMRI, soit par le connecteur de commande DCC externe (J4).
Le signal DCC généré par le microcontrôleur ATmega328 passe par un circuit de puissance (L298N) avant d'être envoyé aux rails afin de contrôler les décodeurs des locomotives et des différents accessoires DCC du réseau.
Matériel nécessaire
Description | Quantité | Référence | Url de recherche |
---|---|---|---|
Condensateur polarisé tantale 1µF | 1 | C1 | condensateur + tantale + traversant + 1µF |
Condensateur 100nF | 4 | C2, C4, C5, C6 | condensateur + céramique + traversant + 100nF |
Condensateur polarisé électrolytique 470µF | 1 | C3 | condensateur + polarisé + électrolytique + radial + traversant+ 470µF + 25V |
Condensateur polarisé électrolytique 10µF | 1 | C7 | condensateur + polarisé + électrolytique + radial + traversant+ 10µF + 25V |
Diode 1N4001 | 8 | D1, D2, D3, D4, D5, D6, D7, D8 | diode + 1N4001 + 50V + 1A |
Pin socket (3x) + pin header coudé (3x) + LED 3mm deux couleurs (vert et rouge), cathode commune | 1 | D9 | led + 3mm + rouge + et + vert + cathode + commune |
LED 3mm jaune (programmation) + Pin socket (2x) + pin header coudé (2x) | 1 | D10 | led + 3mm + jaune |
LED 3mm bleue (exploitation) + Pin socket (2x) + pin header coudé (2x) | 1 | D11 | led + 3mm + bleue |
LED 3mm rouge (détection présence) | 1 | D12 | |
Prise jack femelle d'alimentation 15V 5A montage PCB (5,5 x 2,5mm ou 5,5 x 2,1mm en fonction de la prise du transformateur) | 1 | J1 | 694108301002 + Fiche + jack + alimentation + 6.4mm + Angle + droit + Würth + Elektronik |
Prise d'alimentation des rails (3 broches pas 3,8mm à angle droit pour montage PCB) | 1 | J2 | Phoenix + Contact + mâle + Angle + droit + et + femelle + Droit + 3.81mm + 3 + Pôles |
Prise de connexion aimantée pour la mesure du courant consommé (3 broches pas 2,8mm à angle droit pour montage PCB) | 1 | J3 | Connecteur + magnétique + pcb + coudé + Pogo + mâle + femelle + broche + à + tricoter + à + ressort + THT + pas + 2.2mm + 3 + pôles + 3A |
Prise de connexion aimantée pour les commandes externes (4 broches pas 2,8mm à angle droit pour montage PCB) | 1 | J4 | Connecteur + magnétique + pcb + coudé + Pogo + mâle + femelle + broche + à + tricoter + à + ressort + THT + pas + 2.2mm + 4 + pôles + 3A |
Prise de connexion aimantée de l'ampèremètre (2 broches pas 2,8mm à angle droit pour montage PCB) | 1 | J5 | Connecteur + magnétique + pcb + coudé + Pogo + mâle + femelle + broche + à + tricoter + à + ressort + THT + pas + 2.2mm + 2 + pôles + 3A |
Pin header (2x) de jumper : court-circuiter par un cavalier pour ne pas utiliser l'ampèremètre | 1 | J6 | |
Transistor NPN PN2222A | 1 | Q1 | transistor + PN2222A + TO92 |
Transistor PNP 2N2907 | 1 | Q2 | transistor + 2N2907 + TO92 |
Résistance 0,1 Ohm (2 W) | 1 | R1 | résistance + 0.1 + ohm + 2W + traversante + film + métallique + 1% + chanzon |
Résistance 1K (1/4 W) | 4 | R2, R6, R7, R12 | résistance + 1/4w + 1K |
Résistance 10K (1/4 W) | 4 | R3, R8, R13, R14 | résistance + 1/4w + 10K |
Résistance 2K (1/4 W) | 3 | R4, R9, R10 | résistance + 1/4w + 2K |
Résistance 4,7K (1/4 W) | 1 | R5 | résistance + 1/4w + 4.7K |
Résistance 220 Ohm (1/4 W) | 1 | R11 | résistance + 1/4w + 220ohms |
Bouton poussoir d'arrêt d'urgence (diamètre 16 mm) + Pin header (2x) | 1 | SW1 | Guuzi + 16mm + Bouton + Poussoir + Champignon + Métal |
Interrupteur 4RT de sélection du mode (exploitation / programmation) + Pin socket (12x) + pin header coudé (12x) | 2 | SW2 | Mini + Interrupteur + à + Bascule + 12 + Broches + on/on + 2 + Positions + 4PDT |
Bouton poussoir de redémarrage + Pin header (2x) | 1 | SW3 | |
Interrupteur d'activation détection de présence + Pin header (2x) | 1 | SW4 | |
Arduino Nano v3 + pin socket (15x2) | 1 | U1 | |
Double pont en H L298N | 1 | U2 | |
Dissipateur thermique 25 x 23 x 16mm TO-220 aluminium avec deux picots de fixation | 1 | Dissipateur U2 | Dissipateur + to220 + l298n + 25mm + 23mm + 16mm |
Double ampli OP LM358 + support DIP 8 broches | 1 | U3 | |
Régulateur 5V haut rendement | 1 | U4 | |
Optocoupleur 4N35 + support DIP 6 broches | 1 | U5 | |
Entretoise M3 20mm | 8 | Entretoise + nylon + filetée + 20 + mm + Mâle + Femelle + M3 | |
Vis M3 de fixation de la face du dessus | 4 | ||
Insert M3 (Ruthex) | 4 | Insert + M3 + Ruthex |
Fonctionnement
Génération du signal DCC
Le microcontrôleur ATmega328 de l'Arduino Nano, embarquant une adaptation du programme DCC++, récupère les commandes au format texte via la liaison série et les transforme en signal DCC. Lorsque aucune commande n'est à envoyer, le logiciel DCC++ génère des trames fictives (trames vides ou idle) afin de toujours maintenir le signal de puissance sur les rails.
Circuit inverseur de signal à transistor :
-
un niveau haut du signal d'origine active la base du transistor qui devient passant => le signal inversé passe à l'état bas.
-
un niveau bas du signal d'origine bloque le transistor => un niveau haut apparaît sur la broche du signal inversé.
Toutes les trames générées par le programme sortent du microcontrôleur avec une amplitude comprise entre 0 et 5V. Un montage inverseur de signal (Q1, R6 et R7) permet de présenter au pont en H (U2) les deux formes du signal : la trame émise par le microcontrôleur et le même signal inversé.
Chaque côté du pont en H est commandé par un des deux signaux (origine et inverse). Le circuit de puissance L298N va donc créer un signal DCC en reproduisant le signal d'entrée par l'application alternative de l'alimentation 15 V dans un sens, puis dans l'autre, passant ainsi d'une amplitude 0 / 5 V (signal généré par le Nano) à -15V / +15 V (signal DCC de puissance appliqué sur les rails) :
- 0 V en entrée => -15 V DCC ;
- 5V en entrée => + 15 V DCC.
(Voir le principe de fonctionnement du pont en H)
Le double pont en H L298N, est commandé par le même signal sur ses deux ponts. Ceci permet de connecter en parallèle les deux sorties et bénéficier ainsi d'une puissance doublée. Chaque sortie pouvant absorber un courant de 2A, le branchement en parallèle permet donc de générer un courant DCC pouvant aller jusqu'à 4A (pics à 6A supportés par le circuit L298N).
Protection contre les courts-circuits
Le montage de puissance est alimenté en 15V avec une résistance de shunt en série d'une valeur de 0.1 ohm (R1). La mesure différentielle de tension aux bornes de R1 réalisée par un montage (U3, R2, R3 et C1 ci-contre) autour d'un ampli opérationnel (AOP) permet une conversion du courant consommé en tension qui est présentée sur la broche A0 du microcontrôleur.
Lorsque la tension sur cette broche analogique atteint le seuil paramétré dans le logiciel, la routine de surveillance de la consommation arrête la génération du signal DCC qui est matérialisé par l'allumage de la LED D9 en rouge. Pour redémarrer la centrale, il faut alors envoyer à nouveau la commande de mise sous tension via la liaison série pour que D9 se pare de la couleur verte (génération DCC).
Le coup de poing d'arrêt d'urgence (SW1) connecte directement la broche de surveillance A1 du Nano au 5 V, simulant ainsi un court-circuit sur les rails.
Elements de calculs du montage
Les composants autour de l'amplificateur opérationnel sont montés en amplificateur de tension en régime linéaire à contre réaction négative. Ce nom pompeux désigne en fait simplement un amplificateur de tension linéaire. Il multiplie la tension appliquée sur la broche 3 par le gain du montage et présente le résultat sur la broche 1 (sortie de l'AOP).
- Tension aux bornes de R1 (U = R * I) = 0,1V par Ampère
- Puissance dissipée par R1 pour 4A (P = U * I) = 0,4V * 4A = 1,6W (normalisée à 2W)
- Gain du montage AOP = (R3 / R2) + 1 = (10K / 1K) + 1 = 11
- Sortie AOP pour 4A = tension broche 3 * gain = 0,4V * 11 = 4,4V
Pour une consommation de courant DCC variant entre 0 et 4A sur les rails, la tension à la sortie du montage AOP variera linéairement entre 0 et 4,4V. Les broches analogiques du microcontrôleur mesurent une tension pouvant varier entre 0 et 5V (tension d'alimentation). Cette tension est convertie en un nombre entier sur une échelle de 0 à 1023 par le convertisseur analogique/numérique du microcontrôleur. Une tension de 4,4V correspondra donc à (1023 * 4,4) / 5 = 900. C'est cette valeur maximale qui pourra être paramétrée dans le programme. La constante de courant maximum autorisé, CURRENT_SAMPLE_MAX, ne devra pas dépasser cette valeur de 900 (voir le chapitre concernant les constantes DCC++ plus bas).
Si on désire limiter la consommation du montage à 2A par exemple car il n'y aura pas plus de 7 ou 8 locomotives utilisées simultanément (à l'échelle N), la valeur de la constante sera alors fixée à 450. Il est préférable de toujours ajuster cette valeur au plus proche de la consommation maximum de manière à faire circuler le moins de courant possible lors d'un court-circuit. Si votre réseau s'agrandit et demande plus de courant, rien ne vous empêche de téléverser le programme DCC++ dans la carte Arduino Nano en ayant paramétré une nouvelle valeur de courant maximum.
Sélecteur de mode
La micro centrale DCC offre un mode "programmation" grâce à un sélecteur sur la face avant du montage. Ce circuit ne disposant pas de voie de programmation dédiée dans un souci d'économie des ressources, l'isolation du reste du réseau est réalisée en utilisant le quatrième interrupteur du sélecteur pour couper l'alimentation des rails autour du tronçon de programmation.
En fonction de la position du sélecteur de la micro centrale DCC minimale :
- mode exploitation : les deux tronçons sont alimentés normalement et toutes les motrices sont accessibles via le protocole DCC ;
- mode programmation : seul le tronçon de programmation est alimenté et la motrice présente sur ce tronçon peut être paramétrée sans impacter les autres décodeurs présents sur le réseau.
En alimentant l'ensemble du réseau par l'extrémité d'une voie de garage dédiée à la programmation des locomotives, la micro centrale DCC vous permet :
- De paramétrer une nouvelle motrice déposée sur le tronçon de programmation en lui attribuant un numéro de commande. Puis, après avoir modifié le sélecteur en position exploitation, directement pouvoir la piloter pour l'envoyer à sa destination sur le réseau.
- De piloter le déplacement d'une motrice du réseau vers le tronçon de programmation, puis, après avoir modifié le sélecteur en position programmation, changer le paramétrage des CV de son décodeur. Ensuite, comme précédemment, pouvoir utiliser à nouveau la motrice directement sur le réseau en mode exploitation sans avoir à la manipuler.
Vous pouvez également positionner le tronçon de programmation au milieu d'une voie en isolant chaque extrémité d'un rail de ce segment. En reliant la troisième broche DCC du montage aux deux segments adjacents du rail isolé, le réseau ne sera pas impacté pendant la phase de programmation.
Circuits imprimés
Le montage est composé de quatre circuits imprimés :
- le PCB principal supportant tous les composants de la micro centrale DCC ;
- le PCB de la face avant supportant le sélecteur et les voyants du montage ;
- la face avant présentant la partie visible du sélecteur et des voyants ;
- la face du dessus avec le bouton d'arrêt d'urgence.
Chacune des quatre archives ci-dessous, contient les fichiers nécessaires à la réalisation d'un PCB de la micro centrale DCC modulaire. Vous y trouverez :
- tous les fichiers de descriptions du montage au format gerber (extension gbr) ;
- le fichier de perçage (extension drl).
Chaque archive peut être directement utilisée si vous commandez la réalisation des circuits imprimés à un prestataire (voir le tutoriel Faire réaliser son PCB).
Mise en place des composants
L'ordre d'implantation est toujours le même. On commence par le plus petit composant et on termine par le plus grand :
- les résistances 1/4 W ;
- les diodes ;
- les condensateurs non polarisés ;
- les supports du LM358 et du 4N35 ;
- les pin header ;
- les pin socket (pour le Nano et la platine de commande, insérez les composants qui s'y connectent de manière à obtenir immédiatement le bon positionnement) ;
- les transistors ;
- le condensateur tantale polarisé (attention au sens d'implantation) ;
- les condensateurs électrolytiques (respectez la polarité) ;
- la résistance de puissance qu'il vaut mieux surélever de quelques millimètres afin quelle ne soit pas en contact avec le PCB ;
- les prises DCC et jack ;
- terminez par le L298N sur lequel le dissipateur sera fixé avant la soudure définitive sur le circuit imprimé afin d'optimiser le contact thermique entre les deux composants et faciliter leur implantation. Vous pouvez aussi intercaler un film thermique ou appliquer un peu de pâte thermique entre ces deux pièces pour améliorer encore l'efficacité du système de refroidissement.
Après avoir implanté les composants sur les deux circuits principaux :
- vérifiez visuellement que toutes vos soudures sont réalisées et propres (pas d'oubli ni de soudure sèche) ;
- nettoyez les soudures de la face du dessous avec de l'alcool isopropylique pur pour dissoudre les traces de résines qui n'ont pas manqué de s'accumuler pendant la phase d'intégration des composants ;
- vérifiez la bonne implantation des composants montés sur support (Arduino Nano, LM358 et 4N35) ;
- implantez le régulateur 5V en respectant le sens d'insertion.
Le logiciel chargé dans le microcontrôleur
Le programme DCC++ embarqué dans le microcontrôleur ATmega328 de l'Arduino Nano, cœur de ce montage, est une adaptation de la magnifique version open source développée par Gregg E. Berman. Quelques modifications mineures y ont été apportées afin de l'adapter à la micro centrale :
- les références à l'Arduino Uno ont été remplacées par celles du Nano ;
- les constantes décrites dans le chapitre suivant ont été adaptées aux caractéristiques du montage.
L'archive nommée Micro_DCC_USB_v1-2 correspond au programme DCC++ avec les adaptations citées. Il est donc directement utilisable avec ce montage et peut être téléversé en l'état dans le microcontrôleur.
Téléchargez et extrayez les fichiers de l'archive dans un répertoire dédié, du même nom que le fichier principal (ino), puis :
- Ouvrez le fichier ino dans l'IDE Arduino (tous les fichiers sont chargés dans les onglets).
- Connectez l'Arduino Nano v3 à l’ordinateur par la prise USB.
- Dans l'IDE Arduino (menu Outils), vérifiez la bonne sélection du type de carte correspondant à la carte Arduino Nano et au processeur : Arduino Nano, ATmega328P (Old Bootloader).
- Vérifiez la bonne sélection du port série correspondant à votre ordinateur.
- téléversez le programme dans le microcontrôleur.
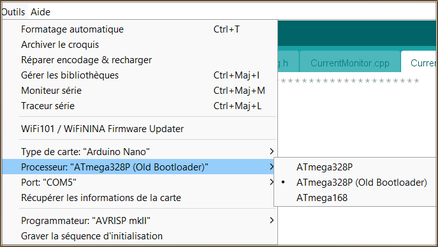
Constantes du programme DCC++ paramétrées pour la micro centrale
Le programme DCC++ est composé de plusieurs fichiers de manière à segmenter et à simplifier la compréhension de l'algorithme pour le programmeur.
Chaque grande fonction de ce logiciel utilise des constantes qui correspondent à des valeurs utilisées à plusieurs endroits dans le code. La constante substitue donc une valeur à un mot clé. L'association entre le nom de la constante et sa valeur (#define <constante> <valeur>) n'est décrite qu'une seule fois. A chaque utilisation de cette valeur, le programmeur la remplace par le nom de la constante.
L'avantage de décrite la constante qu'une seule fois dans l'entête du fichier, permet de n'avoir qu'une seule modification à effectuer en cas d'évolution de cette valeur. Le programmeur n'est pas obligé de parcourir l'ensemble du code pour modifier le nombre à chaque utilisation, au risque d'en oublier...
Après avoir ouvert Micro_DCC_USB_v1-2.ino dans l'IDE Arduino, chaque fichier apparaît dans un onglet. Les constantes ci-dessous sont accessibles dans le fichier correspondant au titre du paragraphe. La modification de ces valeurs a une répercussion importante sur le comportement du programme. Il faut donc les modifier uniquement si on en connait l'impact.
CurrentMonitor.h
#define CURRENT_SAMPLE_SMOOTHING 0.2
#define CURRENT_SAMPLE_TIME 10
Ces deux paramètres permettent de définir le lissage et la fréquence de la mesure de courant. A une valeur de smoothing de 0.1, chaque mesure n'impacte qu'un dixième de la mesure de consommation globale. A 0.5, chaque mesure impacte 50% de la consommation globale. En modifiant le smoothing à 1, le lissage des mesures sera supprimé. Dans ce cas, la prise en compte d'un court-circuit sera plus rapide mais en prenant le risque qu'une mesure erronée déclenche l'arrêt de génération du DCC.
#define CURRENT_SAMPLE_MAX 300
Seuil de détection d'un court-circuit au delà duquel la routine de surveillance arrête la génération du signal DCC (environ 225 par ampère). Pour 4 A, modifier cette valeur à 900.
La valeur par défaut (300) correspond environ à 1,3A, de quoi commencer à faire des tests avec 4 ou 5 locomotives roulant simultanément.
Config.h
#define MAX_MAIN_REGISTERS 12
Nombre maximum de registres pour les commandes répétées.
#define COMM_INTERFACE 0
Paramétrage de la réception des commandes par l'interface série (USB).
PacketRegister.h
#define ACK_BASE_COUNT 100
#define ACK_SAMPLE_COUNT 500
#define ACK_SAMPLE_SMOOTHING 0.2
#define ACK_SAMPLE_THRESHOLD 5
Paramétrage lié aux mesures de courant lors des opérations de lecture / écriture du contenu des CV des décodeurs.
Ces valeurs ont été validées après de nombreux tests sur différents décodeurs.
La micro centrale DCC opérationnelle
Refaisons un rapide point sur l'ensemble des opérations déjà réalisées :
- tous les composants ont été soudés sur le circuit imprimé principal ainsi que la platine de commande ;
- les PCB ont été nettoyés à l'alcool isopropylique pur ;
- un cavalier a été connecté en J3 ;
- la face avant a été connectée au circuit imprimé principal ;
- l'Arduino Nano est connecté à l'ordinateur par un cordon USB ;
- le programme Micro_DCC_USB_v1-2.ino a été téléversé dans le microcontrôleur de la carte Nano ;
- l'alimentation 15V est branchée sur la centrale ;
- la sortie DCC est connectée aux rails.
Le logiciel pilote du réseau : JMRI
En cours de rédaction...
Un boîtier imprimé en 3D pour une finition parfaite...
Le boîtier de la micro centrale DCC modulaire se compose de deux parties :
- la partie basse regroupant les deux circuits imprimés de composants ainsi que la face avant du montage ;
- la partie haute permettant la tenue du boîtier avec la platine du bouton d'arrêt d'urgence.
Si vous ne disposez pas d'imprimante 3D, vous pouvez demander à une société spécialisée l'impression du boîtier pour quelques euros. Il suffira de fournir les fichiers stl contenus dans les archives ci-dessus.
(voir le tutoriel Faire réaliser son impression 3D)
Intégration du montage dans le boîtier
La première étape consiste à fixer les inserts de manière à pouvoir solidariser le circuit imprimé principal au boîtier. Les trous de diamètre 4mm peuvent accueillir tous les modèles d'inserts M3 à implanter à chaud ou aux ultrasons.
Pour une implantation à chaud, la température du fer à souder devra être adaptée au matériau du boîtier :
- FDM entre 350 et 400° ;
- SLA entre 420 et 450° ;
- MJF entre 450 et 480°.
L'étape suivante consiste à mettre en place les trois circuits imprimés sur lesquels les composants sont soudés ou fixés :
- Le circuit imprimé principal ;
- le circuit imprimé de la platine de commande ;
- la face avant du montage.
Les LEDs sont positionnées avant la mise en place des PCB (image à gauche), puis, après avoir été ajustées, sont soudées à la platine de la face avant.
Lorsque les trois platines sont positionnées et les LEDs soudées, les entretoises (8 x 20mm montées 2 par 2) viennent bloquer tous les PCB en solidarisant le circuit imprimé principal avec la partie basse du boîtier.
Le boîtier est prêt à être fermé (image à gauche) après avoir branché le bouton d'arrêt d'urgence sans oublier le cavalier de l'ampèremètre (J5).
La face du dessus permet de solidariser l'ensemble. Elle est fixée aux quatre entretoises reliées à la partie basse du boîtier. Grâce aux trois ergots en haut de la partie haute du boîtier, elle maintient l'ensemble des deux parties qui ne forme alors plus qu'un seul bloc (image à droite).
Pour aller plus loin...
- Téléchargement du logiciel JMRI : Sélectionnez le téléchargement de la suite JMRI en fonction de votre système d'exploitation.
- Aide en ligne de JMRI DecoderPro en français.
- GitHub de la solution originelle open source DCC++ : c'est actuellement le programme open source le plus abouti pour réaliser soi-même une centrale DCC respectant la norme NMRA.
Votre adresse e-mail ne sera pas publiée. Les champs obligatoires sont indiqués avec *.
Commentaires
Ajouter un commentaire